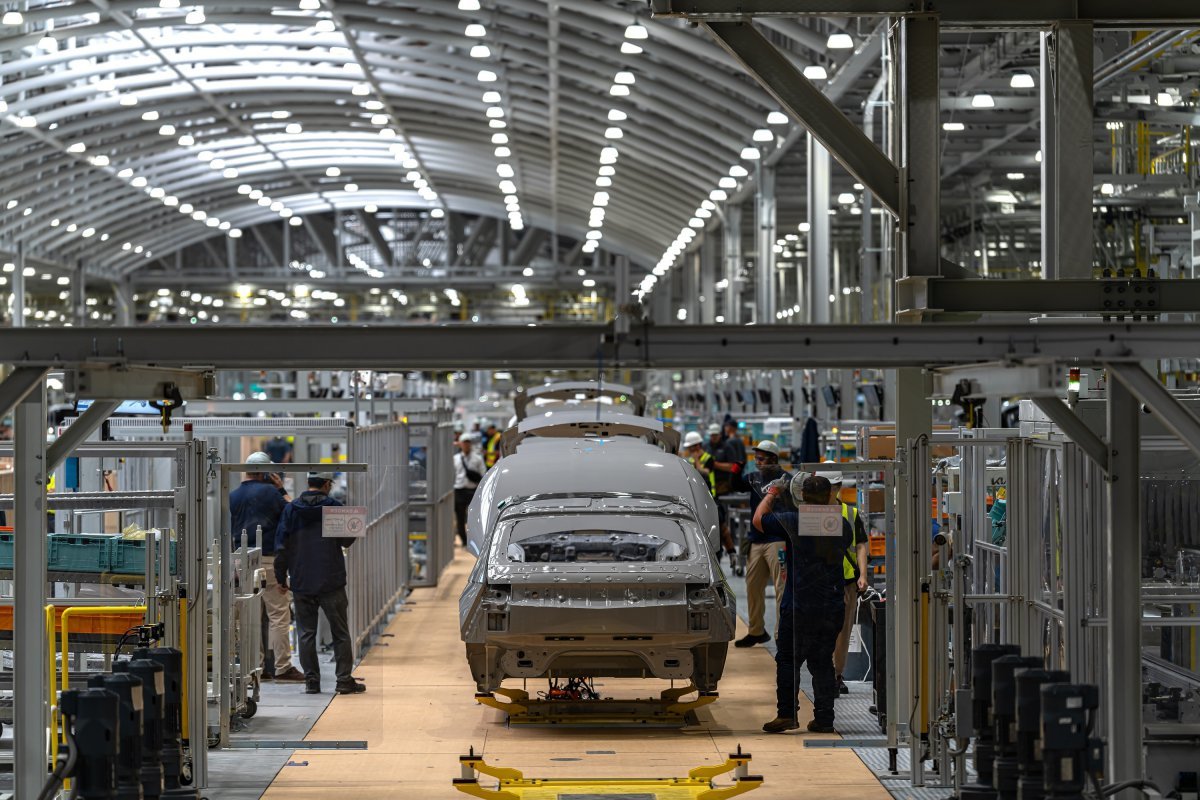
소음만큼 찾아보기 힘든 게 또 있었다. 서울 여의도 4배 크기에 달하는 넓은 공장에 사람도 많지 않았다. 육중한 기계가 스스로 작동했고 바퀴 달린 납작한 운반차가 차체와 부품을 스스로 옮기고 있었다. 메타플랜트에선 고중량 부품 이동 등 근로자가 다칠 수 있는 위험한 작업이나 사람의 눈으로 발견하기 어려운 품질 검사 및 보정 작업을 AI 로봇이 처리했다. 실제로 생산 라인 공정에 투입되는 로봇(950대 이상)이 근로자(880명 안팍)보다 많다고 했다.
앞서 현대차 그룹은 26일 미국 내 최첨단 생산기지인 메타플랜트 준공식을 열었다. 2022년 10월부터 공사를 시작해 2년 반 만에 준공된 이곳은 현대차그룹의 미래 모빌리티 비전이 고스란히 담겨있다는 평가를 받고 있다. 권오충 메타플랜트 법인장(전무)은 “메타플랜트는 현대차그룹이 운영 중인 공장 중 가장 진보된 공장”이라며 “2022년 테슬라 오스틴 공장에도 가봤지만, 메타플랜트가 최첨단 시설을 훨씬 많이 적용했다”고 했다.
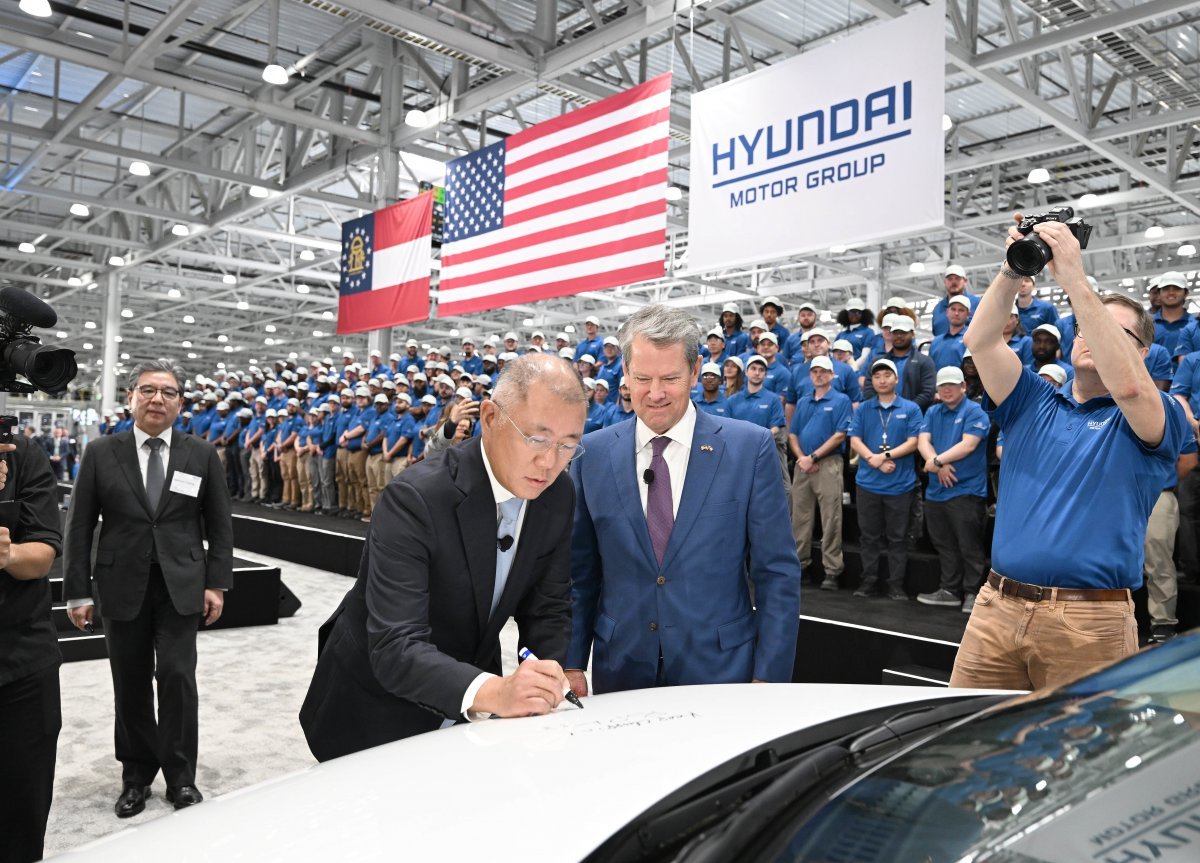
실제로 자동차 제작의 초기 단계인 프레스와 차체 공정에선 사람의 모습을 전혀 찾아볼 수 없었다. 프레스 공정은 납작한 철판을 틀에 대고 기계가 눌러 차량의 외형(패널)을 뽑아내는 공정이다. 기존 공장에선 철판과 찍어낸 패널을 사람이 일일이 나르고 꺼내야 한다. 하지만 메타플랜트에선 6800t의 초대형 고속 프레스 5대가 철판을 내려찍고 자르는 과정을 스스로 수행하고 자동 적재 시스템을 통해 완성된 패널을 사람의 도움 없이 알아서 적재한다. 이 과정에서 AI가 수십 대의 카메라를 통해 금이나 구멍을 포착해 불량 패널까지 걸러낸다.
이렇게 만들어진 패널은 자율주행 운반 로봇(AGV)에 의해 다음 단계인 차체 공정으로 이동한다. 차체 과정에 투입된 AGV만 200여 대다. 메타플랜트의 공정 간 자동차 부품 이동은 전부 AGV가 수행한다. 차체 공정은 패널을 용접으로 이어 붙여 차량의 외형을 만드는 단계다. 차체 공정도 전부 로봇과 기계가 수행해 자동화율이 100%에 이른다. 특히 메타플랜트 차체 공정에선 세계 최초로 로봇과 AI, 비전(Vision) 기술이 차량 문의 간격과 단차를 스스로 보정하는 시스템이 적용됐다. 그 결과 생산 차량간 균일한 단차 품질을 뽑아내는 것이 가능하다.

현대차그룹은 현재 연간 30만 대 수준인 메타플랜트 최대 생산 규모를 50만 대로 늘리기 위해 부지 내에 신규 생산 시설도 구축하기로 했다. 향후 메타플랜트의 생산량을 확대하고 최첨단 생산 기술을 미국 내 기존 공장에도 적용할 예정이다.
엘라벨=김형민 기자 kalssam35@donga.com